Knowing the EPA’s RPP rule can save contractors from big fines and keep homeowners safe
A property owner was recently fined for failing to comply with the EPA’s Renovation, Repair, and Painting Rule (RRP) in regards to lead paint. The owner was fined for conducting work without being licensed or using lead safe practices. This blog will discuss the RRP rule and how to prevent violations.
Basics of Lead Paint.
Lead is a metallic element that was used in paint due to its added durability and brilliance. Prior to 1978, lead paint was a common building material present in the residential properties. According to Illinois and the U.S. Department of Housing and Urban Development (HUD) paint is considered to be lead paint when the material is equal to or above 0.5% (5,000 ppm) lead or 1.0 mg/cm2 lead present. The allowable level of lead was lowered to 0.06% (600 ppm) in 1977 by the Consumer Products Safety Commission. The level was lowered further in 2009 and reduced to 0.009%. Paint in industrial, marine, or bridges may have higher lead levels of lead present. Lead paint becomes hazardous when it is disturbed or begins to deteriorate. The primary concern with lead paint is when lead paint becomes lead dust. The main exposure route for lead dust is via ingestion. Inhalation of lead dust is a secondary exposure route. Lead is less concerning when it is stabilized, in good condition, or encapsulated by newer layers of paint.
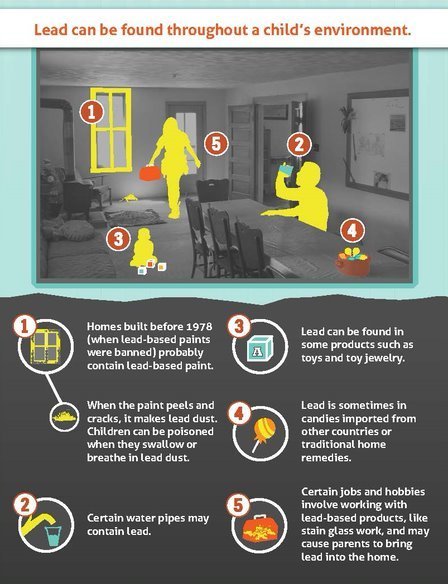
What is the RRP Rule?
The RRP rule was created in 2008 by the EPA and states that workers who may disturb lead in homes, child care facilities, and kindergartens must be certified by the EPA in properties built before 1978. The rule states that workers must follow safe work practices such as sealing off the area, using wet methods, and personal protective equipment (PPE) among many other guidelines. Contractors must attend an 8-hour class and pass an exam. This rule does not apply to homeowners renovating their own properties but the EPA does provide information on best practices for these situations as well.
RRP Vs Lead Abatement?
While many assume that following the RRP is the same as lead abatement, however they are quite different. Both of these activities require training and licensing but that’s one of the few similarities. According to the EPA, lead abatement is a process to permanently remove lead hazard from a property. Whereas with the RRP rule, it is following safe practices while renovating a property. The RRP rule does not guarantee the permanent removal of lead but only seeks to reduce the lead hazards while conducting renovations. Lead abatement requires occupants to not be present, but with RRP the occupants can remain in the home but it is not recommended. Surprisingly, the EPA does not require lead wipe based clearances for RRP, that are typically performed after lead abatement to verify that the work area is not contaminated.
Conclusions
Renovation activities can be a daunting, but making sure regulations are followed for environmental hazards such as lead, asbestos, and other contaminants can prevent fines and potential exposure. Before conducting a renovation, consult with environmental professionals such as Indoor Science to determine if RRP or lead abatement should be used at your property.